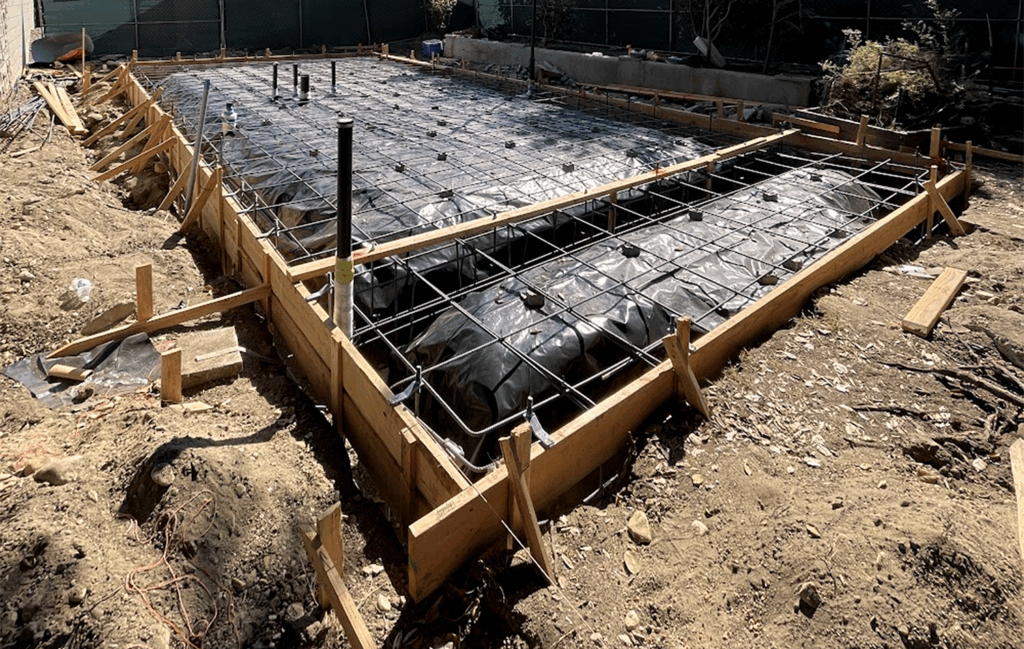
If you’re developing or building in Los Angeles, you may encounter “methane mitigation zones” or “vapor intrusion risk” designations—especially in areas like Bel Air, Malibu, and West Los Angeles near former oil fields or landfills. Gas mitigation isn’t optional; it’s critical for safe, code‑compliant foundations.
What Are Gas Mitigation Systems and How Do They Work?
Gas mitigation systems block harmful gases (methane, VOCs) that migrate through soil into basements, crawlspaces, or slab-on-grade structures. A sealed membrane under the slab plus venting pathways ensures any gas is safely diverted away from occupied spaces.
Core Components of an Effective Gas Mitigation System
-
- Subslab Vapor Barriers: Gas‑resistant membranes laid directly beneath the slab—must be fully sealed and professionally inspected.
-
- Venting Systems: Passive vents use natural airflow; active systems employ fans to extract gas before it accumulates.
-
- Sealed Penetrations & Perimeter Barriers: All pipe penetrations, conduits, and rebar passes must be sealed. Sidewalls, footings, and grade beams are treated to prevent leaks.
When and Where Gas Mitigation Is Required in Los Angeles
-
- Methane Zones: Check the City’s methane zone maps for West LA, Venice, Playa Vista, and Beverly Hills.
-
- Proximity to Landfills & Oil Wells: Historical land use can trigger mitigation requirements during plan check.
-
- Subgrade Structures: Basements, underground garages, and mechanical rooms often need enhanced systems.
Common Pitfalls to Avoid
-
- Skipping methane testing—always submit a soil gas report before design.
-
- Mixing incompatible materials—use components from the same approved system.
-
- Not coordinating with foundation waterproofing—overlaps with protection systems can lead to costly rework.
Benefits of Planning Early
-
- Prevents plan-check delays
-
- Reduces long-term liability
-
- Ensures healthy indoor air quality
Final Thoughts
In Los Angeles, gas mitigation is about more than compliance—it’s about protecting occupants and your project timeline. Partnering with a qualified contractor experienced in shoring, below-grade waterproofing, and environmental barriers ensures complete protection and smoother inspections. Call (818) 540-5235
Explore more at our websites: